Dynamelt™ SR Series - Adhesive Supply Unit
Dynamelt™ SR defines a new standard of innovation in the industry. With intuitive controls and a modular design that make it simple to install, operate and maintain, the Dynamelt™ SR is the go-to choice for manufacturers worldwide. Designed to be used in conjunction with the Dynatec family of equipment for maximum efficiency and performance, this virtually “invisible” system will remain in sight but out of mind in your facility. It consumes 20 % less energy and significantly less air than similar units while advanced diagnostics, quick-change components and a larger filtration surface significantly reduce maintenance cycles and required labor
 |
Overview |
The Dynamelt™ system provides accurate, proportionate temperature control for the hopper, hoses and applicators. Sequential heating delays may be programmed for turn-on of the hoses and heads. A "standby" temperature may be programmed so that the temperature zones can be maintained at a lower temperature when the hot melt adhesive supply unit is not in active use, enabling rapid return to normal operation.
- Simplified access and maintenance procedures make replacing modular electronics, filters and pumps quick and easy.
- Intuitive, easy to read display is repositionable to front or side of unit and shows all system parameters at a glance.
- Consumes up to 20% less energy and significantly less air than similar competitive units, reducing operating costs.
- New Nano ceramic hopper coating is 5 times more durable than competitive PTFE coatings to withstand wear.
- Standard features include 7-Day Scheduler to simplify daily operation.
|
 |
We know that uptime is what really matters, which is why our products are designed with built-in reliability. Patented Melt-On-Demand™ technology is standard in Dynamelt™ hoppers, and the new SR unit filter has 15 times more surface area for longer life and less contamination that can lead to clogged nozzles and downtime. The EVC-1™ is a must-have accessory for applications with frequent line speed changes, as it maintains volumetric glue output to reduce adhesive and product scrap. Gemini™ hoses are the most reliable on the market with built-in dual circuitry to keep your line up and running in the event of a hose failure.
• Melt-On-Demand™ technology
• 15 times more filter surface area
• EVC-1™ ensures consistent output
• Gemini™ hose backup heaters

|
 |
|
|
ITW Dynatec is OSHA VPP Star Certified for impeccable safety, which is always top priority in our facilities as well as those of our customers. The Dynamelt SR™ has multiple safety features such as finger-safe electronics for shock prevention, a lock-out / tag-out main power switch and an insulated heater manifold. When used in conjunction with the ADS1™ delivery system, operators are completely removed from the process of filling a heated hopper, while also eliminating the possibility of spills and slip hazards from loose adhesive pellets on the floor.
• Finger-safe electronics
• Lock-out / tag-out power switch
• Covered manifold
• ADS1 Autofill™ Delivery System

|
|
 |
|
To reduce your total cost of ownership, we have not only focused our innovations on reliability, safety and flexibility but on sustainability over the life of the product. The new Dynamelt SR™ uses 20% less energy and significantly less air than similar units, while advanced diagnostics, quick-change components and a larger filtration surface reduce maintenance cycles and required labor. When combined with our line of BF applicators, Gemini™ hoses, the ADS1™ delivery system and the EVC-1™ volume controller that help to reduce adhesive consumption and additional labor, you have a superior system for a wide range of packaging applications.
• Total system saves you time & money
• Longer maintenance cycles, easy to troubleshoot
• Dynamelt SR™ uses 20% less energy
• Accessories help to reduce labor and adhesive usage

|
|
 |
|
Installation and set-up of your hot melt system needs to be as simple as possible. The new Dynamelt SR™ features corner-mounted hose connections for flexible positioning, a compact footprint for even the tightest of spaces and a display panel that mounts on the front, side or remotely from the unit through a pendant controller. Although the Dynamelt SR™ is compatible with competitive hoses and applicators, the ideal applicator for packaging is the BF Micro™, with it's compact footprint and easy installation. Accessories like the ADS1™ automatic delivery system and EVC-1™ volume controller with smart electronics are simple plug-and-play items that will seamlessly integrate your line.
• Easy installation, compact footprint
• Corner mounted hose connections
• Easy-to-read, repositionable display panel
• Plug and play "smart" accessories
 |
 |
The Dynatec Difference |
Melt-on-Demand Hopper
Most suppliers will agree that adhesive degradation is the number one cause of downtime on hot melt equipment. To address this problem, ITW Dynatec has patented a "Melt-on-Demand" system. ITW Dynatec's vertical, unheated hoppers only melt the amount of adhesive required by the application. Most of the hot melt adhesive in the hopper remains at a much lower temperature, perhaps even solid state. The added benefits of melting only the adhesive required are quicker start-ups, reduced energy costs, better viscosity control, and reduced fumes.
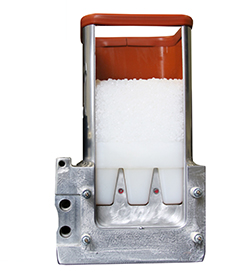
Melt-On-Demand Hopper:
- Less Energy Consumption – The Dynamelt uses less energy than conventional equipment by heating only the adhesive in the lower portion of the hopper. There is no need to waste energy and manufacturing time melting/maintaining the entire contents of the hopper.
- Operator Safety – The adhesive in the top of the hopper remains in a cooler, often solid state and reduces the operator's potential for burns. Also, adhesive splash-back when filling the hopper is reduced.
- Faster System-Ready – The Dynamini Series does not have to melt all of the adhesive, so it is ready for operation much faster than conventional equipment.
- Adhesive Degradation is Greatly Reduced –By only melting the required amount of adhesive, the common problem of charring is minimized. When adhesive is replenished using conventional equipment, the solid, more dense adhesive falls to the bottom of the hopper causing older glue to move to the top of the hopper. By doing this, adhesive is subject to longer heat exposure which is one of the main causes of char. This does not happen with Melt-On-Demand. The molten glue at the bottom of the hopper is used first. Another important benefit is that all of the heat is applied at the bottom of the hopper using Melt-On-Demand, so char build-up on the side walls of the hopper is minimized.
- Reduced Maintenance – With Melt-On-Demand, equipment maintenance will be reduced. Frequency of Periodic hopper draining to purge char is greatly reduced, and filter and nozzle clogging will be reduced as well.
 |
Video: Advantages of the Next Generation Dynamelt S |
Next Generation Dynamelt S Adhesive Supply Unit from ITW Dynatec on Vimeo.